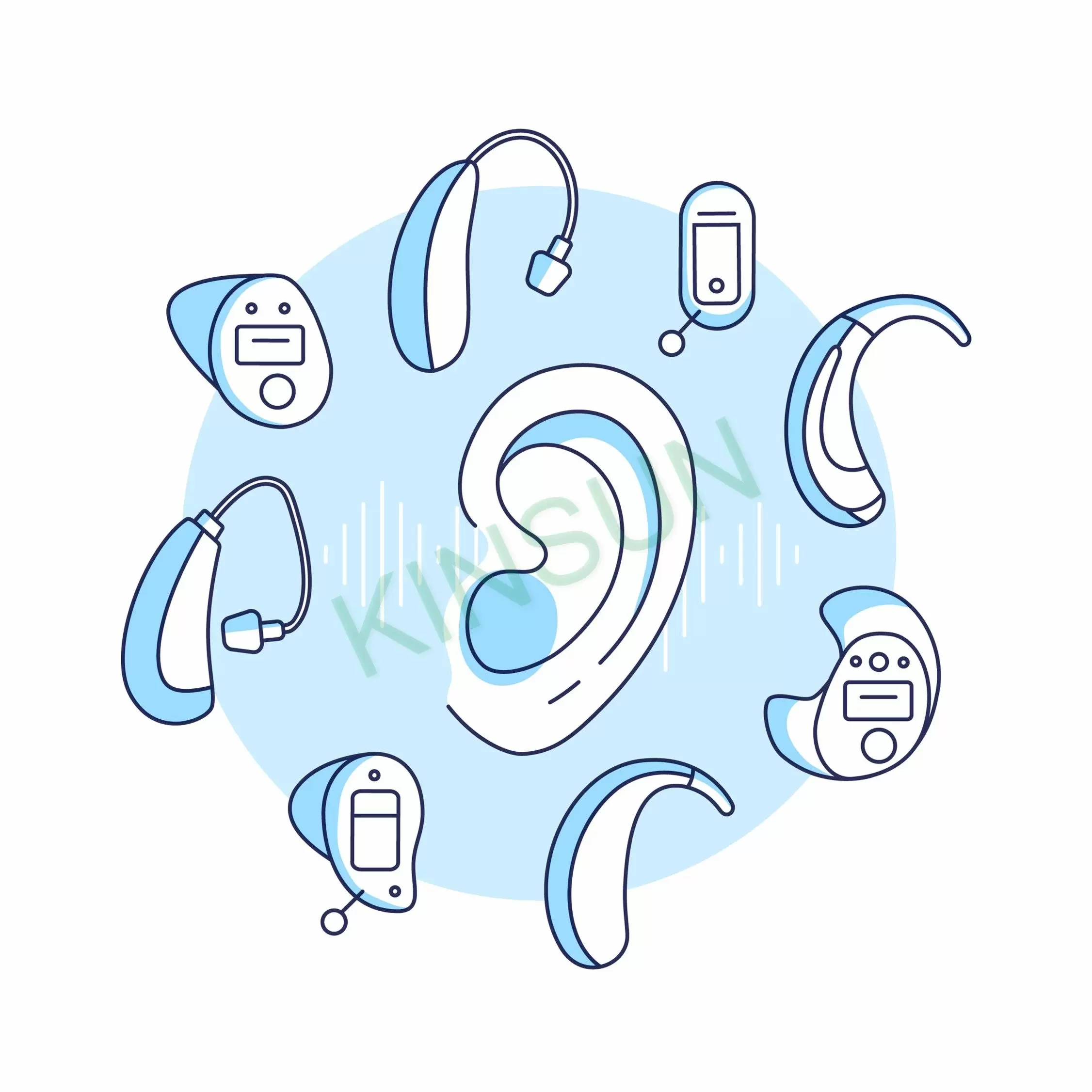
Medical Application
The highly tiny connector for the medical device
Kinsun is an expert in providing custom medical connectors and components. With over 35 years of experience designing and manufacturing, we can offer advanced medical connectors in various medical devices, including hearing aids, electric medical beds, blood glucose testers, surgical instruments, and dental and orthopedic devices. Strict production control and professional manufacturing practice can help meet customers' requirements and quickly bring their ideas to reality.
Case Study
The role of the connector in the hearing aid can transmit the audio signal to the amplifier, and the hearing impaired can then hear the sound from the outside world. And because of the request of pursuing extreme lightness and miniaturization, the size of the connector must be very tiny while achieving durability in daily use. Therefore, when evaluating the project, the customer wanted to find a manufacturer competent in stamping and plastic micro injection molding and can provide advice to the customer's original design to fit the mass production before making dies and molds.
Advantages of Kinsun
- The profound experience and knowledge in manufacturing and developing dies and molds help to meet the customer's requirements for strict quality and quick development time.
- With the accuracy of 0.01mm precision plunger metering pump of the full electrical plastic micro injection molding machine, complementing the 0.01mm thickness stamping capacity, we can achieve the tiny volume of connectors, which can be less than the size of a grain of rice.
- Full labor force and automatic production can meet the customers' pressing schedules.
- 100% inspection of dimensions check and conductivity test before every shipment.
Project Implementation
The project took one month to assess before it officially went into development. After one year of a series of sample tests and certifications at both Kinsun and customer's side, the pilot production began, and three months later, the series production kicked off. And shortly after, the production ramped up.
Manufacturing Challenges
- The first challenge was that the connector was just too small. It was the most miniature waterproof product Kinsun has ever built, which brought the manufacturing much difficulty. In light of this, we use microscopes to operate during wire trimming, soldering, inspection, etc., instead of using traditional assembly by the naked eye.
- There is a miniature electrical circuit inside the connector. Because the electrical circuit is too delicate and tiny, chances are the injection molding pressure can damage it. Therefore, to protect the electrical circuit, the engineers worked out numerous manners before it succeeded.
- Moreover, there was nearly 30% of high defect loss initially. After adjusting and improving the manufacturing processes, the rate is now effectively controlled under 0.02%.
- Additionally, it came along with the low yield with 2-3K pieces, so we expanded the labor force and figured out which workstations could be improved. E.g., we found that attaching the sealing gasket to the connector by hand took so much time. To replace the time-consuming task, we introduced the Liquid Silicone Rubber (LSR) injection molding machine, which can straight mold the gasket on the connector. After a series of adjustments, the volume now can be 10K per day.
Conclusion
Because the product's launch schedule was pressing, here at Kinsun, there have been round-the-clock work and countless interdepartmental meetings. Although there had been numerous hurdles, eventually, they were overcome with our team's effort. Most importantly, it is all worth it when we can meet the strict quality and on-time delivery.